101 Ways to Improve Your Lubrication Program
101 things you should know to develop a world-class lubrication program. Whether you are in the initial stages of implementing a new program or already have a well-established program in place, you should find numerous ideas that can help, with advice from each of the 101 issues.
1. Be Proactive
When applied correctly, a proactive maintenance strategy can double or triple lubricant service life. This is achieved by reducing the conditions that stress an oil (cleaner, cooler, drier, etc.).
2. Know Your Lubrication Needs
The next time you award a supply contract for lubrication, take the time to actually determine your company’s needs. The process may reveal that you have been paying for services that you don’t value or would prefer to buy elsewhere.
3. Skills Foster Reliability
If what you want most is to avoid machine failure, then what you need most are maintenance skills that foster intrinsic machine reliability.
4. Set Target Cleanliness Levels
The first step of a contamination control program is to identify a machine’s target cleanliness level. A specific quantifiable number (ISO Code, for instance) should be assigned to each machine based on contaminant tolerance, operating environment and motivation for machine reliability.
5. Design Simple Lube Inspection Routes
Design lubrication inspection routes comprised almost entirely of questions that the inspector can answer “yes” or “no,” or as “OK” or “not OK.” This keeps the process fast and simple.
6. Replace Business as Usual
Achieving lasting excellence in machinery lubrication is neither difficult nor complex. It simply requires a clear sense of purpose and the tenacity to replace the old business as usual with a new one.
7. Consider Single-point Lubricators
Depending on the application, single-point lubricators can extend the life of rotating equipment and increase reliability while significantly reducing the cost of applying the lubricant.
8. Use Performance Metrics
If used properly, a performance metric works like a compass. It helps you find your bearings and get on the right track when performance is substandard. Once the organization is performing on target, metrics help to keep it on track and facilitate continuous improvement.
9. Follow the Root-cause Trail
Machines don’t just die; they’re murdered. If you follow the root-cause trail, you will likely find a smoking gun in the hands of one or more well-intentioned individuals (operator, craftsman, technician, mechanic, engineer, etc.) who simply didn’t know any better.
10. Achieve a Cultural Transformation
No single product or training course will accomplish cultural transformation because people resist change by nature. A cultural transformation requires a clearly defined and cohesive plan that may take a considerable period of time to fully accomplish.
11. Requirements for a World-class Lube Program
The best lubrication programs, often referred to as world class, are those that have world-class lubrication technicians, use world-class lubricants and deploy world-class procedures.
12. Collaborate for Lubrication Excellence
Lubrication excellence is a collaborative process. By taking an active role in testing new lubricants and giving constructive feedback to your supplier, incremental improvements in lubricant quality are bound to result.
13. Don’t Waste Your Money
Saving money by buying cheap oil is almost always a false economy. On the other extreme, buying quality oil to remedy bad lubrication is also a false economy.
14. Know the Dangers of Grease Incompatibility
Contemplating a switch of grease products brings to light the critical issue of compatibility. Before implementing a new product, plant and maintenance engineers must weigh all consequences of grease intermixing and the impact on equipment reliability, production levels and the bottom line.
15. Plan and Research for a Better Lube Room
A world-class lube room is not built overnight. The planning and research required are more time-consuming than the actual construction work.
16. The Importance of a Good Education
Training and education develop top-drawer lubrication skills and can give the dollop of grease and the rolling-element bearing a long, happy life.
17. How to Sell Your Project
It is incumbent upon the lubrication professional to translate a technically oriented program proposal into results that a manager understands and values. Whether you are selling your project to the executive suite or the maintenance managers, fit the message to the audience.
18. Ensure Fluid Cleanliness
Maintaining fluid cleanliness is a job that’s never done. It involves a relentless cycle of sampling and remedial action as necessary to ensure the appropriate cleanliness level is continuously maintained.
19. Slow Down When Applying Grease
Do not rush the application of grease, as this can lead to oil bleeding in the feed line. Instead, apply using a constant force. Also, if the action is too fast, grease will leak at the labyrinth seals.
20. Detecting Bearing Distress
Through the prudent use of temperature and vibration monitoring equipment, routine oil analysis, lubrication system evaluations and machine operational performance reviews, bearing distress may be identified and evaluated before catastrophic failure occurs.
21. When to Outsource Lubrication
Under the right circumstances, when machinery lubrication is outsourced to create value and competitive advantage, not just to cut costs and/or window-dress the organization, it can be a winning strategy. It can help foster or perpetuate a “best-in-world” attitude.
22. Beware of Overheated Hydraulic Systems
Continuing to operate a hydraulic system when the fluid is over-temperature is similar to operating an internal combustion engine with high coolant temperature. Damage is guaranteed. Therefore, whenever a hydraulic system starts to overheat, shut it down, identify the cause and fix it.
23. Invest in Reliability
Improvements made to assure proper lubrication of your equipment will yield benefit regardless of its age. However, early, reliability-focused investments to build a lubrication program that works and to accessorize equipment for lubrication excellence will compound over time and maximize your returns.
24. Understand Wear Modes
It is estimated that 70 percent of machines are removed from service due to degradation of mechanical surfaces. Degradation may occur as a result of abrasive, adhesive, erosive, corrosive or fatigue-induced wear. A clear understanding of how these wear modes develop will assist the lubrication technician in understanding the importance of his/her role in improving machine reliability.
25. Make Oil Filters Last Longer
Oil filters last longer when they don’t get plugged with particles. Therefore, the best strategy comes from working backward by tracing the particle ingression pathway.
26. The Key to Lubrication Program Success
While there are a number of excellent companies that offer outstanding products and services to support precision lubrication, it is the people - and more importantly their attitudes and the pervasive culture within the plant - which will do more to help the success or failure of the lubrication program than any other single factor.
27. Select the Right Lubricant
Selecting the proper lubricant is important to sharply reduce long-term costs. The best-fit product selection can mean longer lubricant life, reduced machine wear, reduced incipient power losses and improved safety.
28. Keep It Simple
Excellence in lubrication is a simple concept. It is about getting the right lubricant in the right place at the right time, making sure that lubricant is supplied in the right quantity and ensuring the lubricant is kept clean, dry and cool.
29. Follow Manufacturer Instructions
When relubricating electric motor bearings, always follow the motor manufacturer’s specific instructions and do not use any lubricants other than those approved by the manufacturer.
30. Paying for Performance
Properly selected high-performance lubricants may create cost reductions many times greater than the price differential between the product types. Selecting a performance option should be based on the effect derived from a carefully engineered change, with the expected results calculated into commonly accepted financial terms.
31. Don’t Blame the Lubricant
The universal panacea to a real or perceived lubrication failure is to blame the lubricant. Naively, we go looking for a better lubricant, when in actuality it may simply be how lubrication is performed that is at fault.
32. The Value of Oil Analysis
If used correctly, oil analysis can be a valuable predictive and proactive diagnostics tool. If used incorrectly, it can be a frustrating exercise in futility.
33. Match the Lubricant to the Application
Selecting lubricants for industrial gearing is similar in most applications. To identify the best choice for a given application, the right viscosity, base oil and type of lubricant must be selected and the appropriate performance properties evaluated.
34. Knowledge Is Power
When decisions are made to make improvements to your lubrication program, it is crucial that you decide what knowledge and to whom it must be disseminated to facilitate and ensure the quality of implementation and execution of these items.
35. The Importance of Proper Sampling
Without proper sampling methods, the value of oil analysis will be lost or severely diminished. The problem often lies in inconsistent and invalid data. Unless you can take consistent, repeatable samples, it is impossible to establish useful alarms levels.
36. Use Your Senses
An effective proactive/predictive maintenance program requires tools such as vibration, thermography and oil analysis to scan, inspect and determine the condition of machinery. However, your eyes, ears and nose can also be valuable condition monitoring tools and require little training to be utilized effectively.
37. Make Better Use of Filter Carts
Portable transfer/filter carts are versatile and can be used for more than just transferring fluids. Other possible uses include offline filtration, cleaning stored lubes, flushing after machine repair and rebuild, flushing during equipment commissioning and draining a reservoir or sump.
38. Prevent Lubrication Mistakes
How can you error-proof against lubrication mistakes? One obvious way is through tagging - applying color- and shape-coded tags to machines, transfer devices and storage tanks to ensure that the wrong oil or grease is not accidentally added.
39. The Drive for Cleaner Fluid
Fluid cleanliness is really no different than driving: They both require a clear understanding of the target, an ability to validate the target is being met, and a mechanism to take correct action when a deviation is observed.
40. Establish Lube Procedures
Lubrication procedures often vary from technician to technician based on convenience or preconceived notions of best practice. These methods of personal choice can depart significantly from OEM- or industry-defined best practices. The correct procedure needs to be established and routinely applied.
41. You Can’t Buy Lubrication Excellence
Don’t be lulled into a false sense of security that you can buy your way to lubrication excellence. Think about lubrication excellence as a change in the process of lubrication, rather than a solution that can be purchased, set and forgotten.
42. New Oil Is Seldom Clean
In the majority of cases, new oil is not suitably clean for most applications. Whether tote tanks, drums or bulk tanks are used, it is usually simple and inexpensive to install high-quality filters at the dispensing station to achieve a desirable cleanliness for the new oil.
43. Benefits of Storing Oil in Bulk Tanks
It is often easier to maintain low particulate contamination levels when oils are stored in bulk tanks because they are normally closed to the atmosphere and the oil is dispensed via a pump or tap.
44. Manage the Life Cycle of Your Lubricants
To extract the maximum value from lubricants and the lubrication program, lubricants must be properly managed from cradle to grave. This means adopting best practices for receiving, storing, dispensing, maintaining and finally disposing of used lubricants.
45. Eliminate Air in Lubricated Systems
It may be impossible to completely eliminate air from lubricated systems, but steps should be taken to reduce it as much as can reasonably be expected. Eliminating excessive air will likely give more life to your oil, improve system performance, and reduce wear and deposits.
46. How to Schedule Oil Changes
Don’t schedule oil changes on large volumes of lubricants unless your oil dictates the need. Deploy oil analysis to determine the need and timing of the oil change instead of the calendar.
47. A Winning Combination
Reliability emerges from the optimum combination of quality lubricants and best-practice lubrication. Don’t spend more money on premium lubricants hoping you can spend less on lubrication. There is no substitute for vigilant inspection, frequent and thorough oil analysis, and well-deployed lubrication practices.
48. Keep Tabs on Oil Filters
Keeping tabs on the performance of oil filters is essential to machinery reliability. Yet too often, many people in the maintenance field seem to be oblivious to the importance and methods of doing so. The best strategy is a proactive strategy.
49. Evaluate Your PMs
Preventive maintenance is among the most common root causes leading to the need to perform corrective maintenance. It need not be. Evaluate your PMs and eliminate tasks that fail to add value or actually create failure.
50. What to Consider Before an Oil Flush
The risks of not performing a needed oil flush include oil starvation from line restrictions and motion impediment of critical machine parts. And, postponing a needed flush can make matters substantially worse. Therefore, before planning and performing an oil flush, know the pitfalls and countermeasures.
51. Expand Your Wear Debris Universe
Take wear debris analysis to another level by digging deep to expand your wear debris universe. Develop new in-house skills and tactics that enable weak signals to be detected and virgin particles to be found and analyzed.
52. Monitor Water Contamination
Water is one of the most destructive contaminants in oil, and it would serve you well to monitor it on a consistent basis when dealing with sensitive or critical equipment.
53. Know the Bearing Type
Know the type of bearing being lubricated. A sealed bearing can’t be regreased. Shielded or double-shielded bearings can be greased but slowly so as not to overpressurize the cavity and push the bearing shield against the cage.
54. Send the Right Signals
Sealable and reusable (S&R) containers serve as a visual sign of maintenance excellence. Conversely, use of fossilized oil cans serves as a constant reminder of maintenance neglect and program stagnation.
55. Use the FIFO Method
For both oil and grease, be aware of their respective shelf life. Exceeding OEM shelf life may render the product useless or severely hamper its performance. For this reason, it is best to use the first-in, first-out (FIFO) method.
56. Develop Lube Guidelines
Lubrication instructions need to provide guidelines that are simple and easy to understand but also contain specific details for how to perform a task according to prescribed best practice.
57. Employ Dynamic Route Planning
Instead of walking to and from the lube room, locating and gathering different tools, and handling paperwork before executing the work, employ dynamic route planning, which allows those tasks that logically fit together to be done at the same time, no matter what their prescribed frequency.
58. Make Lubricant Consolidation Easier
It can be difficult to consolidate lubricants based solely on their names, but when considering their performance properties, the consolidation efforts are clearer and easier.
59. Add a New Dimension to Oil Analysis
Effective oil analysis may be as much about data presentation as it is about the data itself. By leveraging the full resources of computer software, including multimedia, oil analysis can take on a whole new dimension.
60. Design a Better Lube Room
A properly designed lube room must be functional, safe, expandable and provide all necessary storage and handling requirements for the facility. Lube room designs should allow the maximum storage capacity without allowing for too much bulk oil and grease storage.
61. Consider Machine Criticality
Be fully aware of machine criticality. Changing the use or specification of lubricants in mission-critical equipment should not be done without skillful engineering.
62. Dangers of Overgreasing
Overgreasing can have many of the same negative side effects as undergreasing, plus the added cost of high lubricant consumption. Do not exceed the properly calculated amount of grease when performing greasing activities.
63. Continuously Improve Your Lube Program
A lubrication program needs constant refinement and continuous improvement. It is easy to slide back to the old ways of doing things if not careful, especially if the organization has a high turnover rate in the labor force.
64. Handle Oil Drums with Care
Avoid damage to oil drums and other large containers during handling. Negligent handling can cause leakage or ingression of dirt.
65. Make Modifications for Reliability
Lubrication-enabled reliability is not high science. Any maintenance organization can accomplish it with proper training, planning and deployment. Much of it is behavior based and just good old common sense. It’s about making modifications of people, machines, procedures, lubricants and metrics.
66. The Value of Machine Inspections
Simple inspections on all types of machines provide invaluable information as to their condition as well as reassurance that they are operating in a reliable manner.
67. Check Your Additive Package
Whether they are enhancing, suppressing or imparting new properties to the base oil, additives play an important role in the lubrication of machinery. When the additives are gone, they’re gone, so don’t forget to check your additive package.
68. Not Just Any Lubricant Will Do
Machines don’t just need some lubricant or any lubricant. Rather, they need a sustained and adequate supply of the right lubricant.
69. Know the Factors That Influence Oil Life
The end of oil life is influenced by a complex array of factors. Many of these can be monitored, controlled and used to optimize the oil drain interval.
70. Check Sight Glasses
It’s not enough just to put a sight glass on a machine and walk away. These devices should be monitored. They are windows into what is happening with your oil and can give you a first-hand account of any problems that are occurring.
71. Keep Oil Clean
Keeping the oil clean is the first order of business if extended oil replacement intervals are the goal. In turn, achieving extended oil replacement intervals often makes it economical to use superior-quality synthetic lubricants.
72. Advantages of Hard-piping Machines
Hard-piping machines to a fixed oil supply is one way to address a lack of available labor to handle oils. Since this reduces the number of hours it takes to perform an oil change, the plant can run more efficiently with the staff it already employs.
73. Contamination Control Advice
The control of contamination in machinery is pointless if contaminated or below-specification lubricants are used, or if clean lubricant is being handled so carelessly that it enters machines in a contaminated state.
74. Create Electronic Lube Procedures
Get your lubrication procedures in an electronic form, preferably on your company-wide intranet or onto an internet account for those moving toward web-based application support. When procedures are electronic, they can be updated globally, attached to work orders and linked to like machines in your computerized maintenance management system.
75. Add Accessories
If you truly want to make strides toward becoming a world-class program, you will need to make equipment modifications. By adding accessories such as desiccating breathers, quick connects, external level gauges and sample ports, you can transform a small gearbox to world-class standards in terms of contamination control, maintainability and reliability.
76. Share Responsibility for Reliability
Reliability needs to have shared responsibility. It must be fixed in the DNA of the machine as well as in the minds of operators and maintainers. It’s like a reliability chain – every link in the chain must be equally strong for the chain’s full length to bear the load.
77. Monitor Wear Debris
By vigilant monitoring of wear debris as well as understanding the forces at play during the break-in period, you can ensure that your machines will have a longer life and experience fewer breakdowns.
78. Don’t Neglect Lubricant Disposal
Proper handling techniques do not end when the oil has been put into service. Once the life of the oil has been exceeded, you must ensure the lubricant is captured and disposed of both safely and in an environmentally friendly way.
79. Manage Change
Your lubrication strategy will depend on the scope of the project, the size of your company and the cultural maturity of your organization. The bigger the organization and the project, the more relevant a good change-management initiative becomes, and the more resources will be needed for a seamless and faster implementation.
80. Ensure Multiple Sampling Locations
Most circulating and hydraulic systems should have both a primary and secondary sampling location to ensure that any identified failure mechanism can be tracked back to the component causing the problem.
81. Value Knowledge and Skill
Make education and job competency a big deal. Knowledge and skill should be appreciated, respected, celebrated and reinforced. Use education as a team-building tool to bring people together with shared goals and create opportunities for coaching.
82. Control Leaks
Leakage control makes good sense for a number of reasons. Not only are there lubricant consumption savings but also reliability and safety benefits.
83. Trend Oil Analysis Data
Simply obtaining a snapshot of data from an oil sample is essentially worthless without something to which to compare it. This is why trending data in oil analysis reports is so beneficial. It not only allows you to determine if the current oil properties are unfavorable but also if they will become unfavorable in the near future.
84. Visit Your Lubricant Blender
If you have the opportunity, visit your blender’s plant and check out their processes. See if they are putting the same emphasis on keeping lubricants clean as they are on blending and formulation specifications.
85. Match Synthetic Oils to Machinery Needs
Synthetic oils can be tremendous assets to any lubrication program, but they must be matched to the machinery’s needs to get the optimum benefit from them. When making the transition from mineral base fluids to a synthetic base, be sure to flush the system to minimize any residual compatibility issues that may remain.
86. Develop a Plan for Used Lubricants
All plants should have a coordinated plan for managing used lubricating oil, including how much oil is reclaimed and how much is recycled.
87. Emphasize the Reasons for Change
When implementing change, such as when designing or redesigning a lubrication or reliability program, people need to know why the change is being made and how it will affect them. Understanding the need for change is the first step in creating new behaviors within a facility.
88. Question Viscosity Recommendations
Don’t assume the lubricant in your machine has the right viscosity simply because it is the one specified in the machine’s service manual. Challenge conventional recommendations for viscosity. Some machines are operating at conditions far afield from that intended by the machine designer.
89. Identify the Cause of Oil Leakage
Any time there is oil leakage in a system, there’s a reason for it. The entire system should be analyzed, and the cause of the leaks identified.
90. Handle Lubricants Carefully
Most lubricants should be handled with care and proper personal protective equipment (PPE). Create a barrier between you and the lubricant. Wear gloves and safety glasses as well as oil- or chemical-resistant boots. If possible, keep all exposed skin covered.
91. Determine the Correct Oil Level
The best time to decide on the appropriate oil level for your equipment is when the machinery first arrives at your facility. Once the correct oil level is identified, it must be clearly marked in the field.
92. Watch for Foam
Contaminants frequently affect a lubricant’s foam tendency and stability as well as water separability. If you detect more foam than normal or demulsibility issues, it may be an indicator of lubricant contamination.
93. Find the Source of a Heat Problem
The next time a heat problem occurs in one of your systems, look for oil that is flowing from a higher pressure to a lower pressure in the system. That’s where you’ll likely find your problem.
94. Keeping Oils Fluid
In some applications, it is nearly impossible for oil to remain fluid at all ambient temperatures. In these situations, the use of an oil heater is recommended.
95. Consider Water-based Fluids
Water-based fluids are an alternative when fire resistance is imperative and typical lubricant properties like viscosity or lubricity are less important.
96. Test New Oils
It is critical to your oil analysis program that you sample and test oils upon receipt. The possibility of receiving the wrong oil or lubricants that do not meet the required specifications is very real.
97. Choose the Right Lubricant to Reduce Air Pollution
One of the more overlooked aspects of a lubricant is its ability to influence environmental emissions. By selecting the proper oil, you can help to reduce some of the harmful contaminants that are spewed into the environment without sacrificing the needs of the machine or the performance of the lubricant.
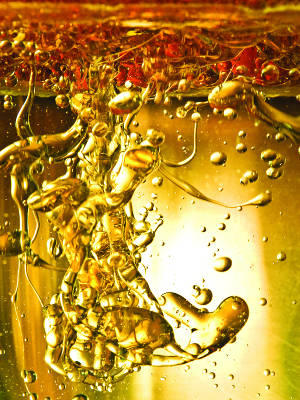
98. Invest in Training
Even if you have invested large amounts of resources in your program, you may still need to invest in training for your team members in order for them to execute your procedures properly.
99. Check Your Oil Analysis Lab
Most oil analysis practitioners assume the data from their laboratory is accurate and irrefutable, but this may not always be the case. Routine checking of your lab is crucial.
100. Water Contamination Can Affect Oil Viscosity
A common misconception is that water will reduce the viscosity of a lubricant. In fact, if an excessive amount of water is “whipped” into the oil in such a way that it forms a stable emulsion, the viscosity can increase, sometimes dramatically so.
101. Certification Provides a Host of Benefits
A good lubrication certification program includes competence that is not only specialty-specific, but also focuses on core abilities (application-oriented) and establishes and validates a standard skill level for practitioners. Certification increases confidence, proficiency and performance (know-how applied).