A History of Oil Analysis
In this, the first of our monthly history series, we will look at the inception and rise of oil analysis. Specifically, we will be looking at the development and implementation of elemental spectroscopy, ferrography and infrared spectroscopy.
Lubricants have been inspected and monitored for perhaps as long as they’ve been in use. But until the second half of the 20th century, inspection and monitoring was limited to temperature, pressure and the occasional check for oil colour and viscosity. There are also references to blotter spot testing of in-service lubricants in the late 19th century.
Prior to the widespread use of routine oil analysis for condition monitoring, there were numerous methods to examine the physical, chemical and performance properties of new lubricants. These properties included viscosity, flash point, pour point, density, total insolubles and water contamination. These early tests were promoted by oil companies as a way to characterize the basic properties of different lubricants and to ensure the quality of their product. These tests also served the purpose of legally defending the lubricant manufacturer in the event of machine failure.

Between 1946 and 1948, the Denver and Rio Grande Railroad began using elemental spectroscopy to test lubricants for the abnormal presence of wear metals, namely aluminium, copper, iron and lead. This practice was implemented with the interest of avoiding accidents and reducing mechanical failure. The focus on wear metals can be credited for a paradigm shift regarding lubricant testing, shifting the focus (although not entirely) from testing lubricant health and performance to monitoring machine health. This effort aimed at reliability was successful, and other railroad companies soon implemented similar practices.
Early Use of Elemental Spectroscopy
Early elemental analysis done by the railway industry utilized atomic absorption spectroscopy. It was a slow, tedious bench testing method performed one metal at a time. Because of this, wear metal analysis remained largely confined to the railway industry until the late 1950s, when Dr. Walter Baird, president of Baird Automatic, Inc., invented the semi-automatic atomic emission spectrometer (AES). This device, commonly referred to as the Baird Spectrometer, offered quick, multi-elemental analysis of fluids, reducing the amount of time required for testing from hours to minutes.
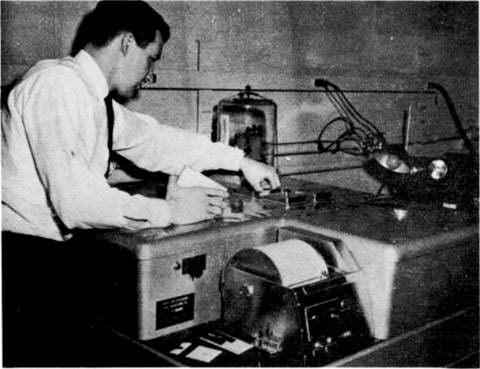
The initial scope of his new spectrometer was railroads and large industrial plants. These were organizations that would most benefit from speedy oil analysis. But automated spectrometers made it possible for a commercial market for the new technology to emerge. In the 1960s, Edward Forgeron, a physicist and sales manager at Baird Atomic, Inc., saw the potential of the technology. He envisioned a laboratory equipped with AES that could receive and test samples from various user organizations around the country. Analysts, Inc., in Oakland, California, became the first lab to offer AES for in-service lubrication analysis in the United States.
Continued Development
In the late 1960s, United States military aircraft were experiencing failures due to rolling element bearing fatigue. The particle detection technology used by the military at the time were ferromagnetic chip detectors and elemental spectroscopy. Neither of these methods was effective at detecting small particles associated with the early onset of bearing wear — they could only provide an alert to advanced, impending or precipitous bearing failure conditions.
To remediate this problem, at least in part, the U.S. military contracted Vernon Westcott, founder of the Trans-Sonic Corporation, to develop an alternate technology. In the early 1970s, Westcott introduced the ferrograph as a new laboratory instrument to visually detect and analyse particles of all sizes. Initially, the ferrograph was used by universities, including Oklahoma State University and the University of Swansea (Wales).
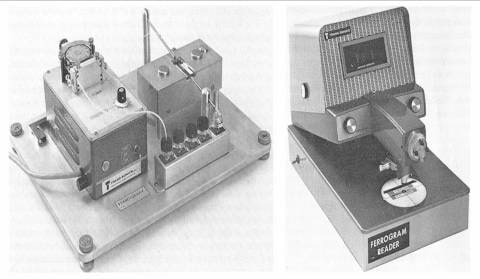
In the early 1980s, more widespread acceptance of the ferrograph was seen, especially by the military. For instance, ferrography was used by the British to predict helicopter transmission failures during the Falklands War. Ferrogrophy also gained popularity in the private sector. In 1982, the first International Conference on Advances in Ferrography was held.
Westcott and his colleagues continued to research and develop better methods of using ferrography, eventually developing analytical ferrography followed by direct-reading ferrography. The latter was an especially helpful development, as it revealed the ratio of small to large particles, allowing wear to be more easily quantified.
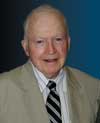
Around the same time, there were other advances in used oil analysis. For instance, Fourier transform infrared spectroscopy (FTIR) began to enter the oil laboratory scene. This type of spectrometer provided quantitative and qualitative information on oil chemistry and certain contaminants, not wear metals. Unlike an atomic spectrometer that looks at atoms, FTIR spectrometers are molecular. They can detect abnormal changes in base oil and additive chemistry, including oxidation, nitration and sulfation. Water, soot, fuel dilution and antifreeze can also be detected.
As new instrument technology began to flood the field of oil analysis (and other applications in analytical chemistry), the cost of performing quality analysis began to fall. In the 1990s, pattern recognition through the use of particle imaging software also became available, allowing for computer-enabled wear debris characterization. Charge-coupled devices (CCDs) also found use in particle counters and other instruments.
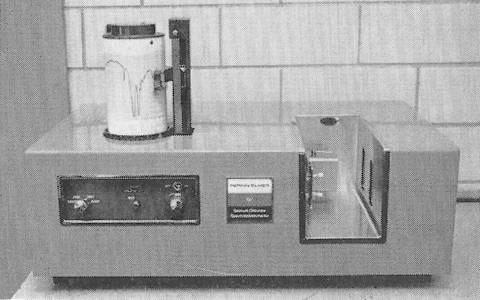
Around the turn of the century, online and onsite testing began to become more prevalent, largely due to advances in sensor technology and the availability of smaller, more portable instruments. As the first decade of the 21st century progressed, so too did oil analysis technology. The end of the decade saw the introduction of semi-portable and affordably priced analyzers as well as handheld IR spectrometers. As we enter into the third decade of the century, attention is being focused on artificial intelligence and the Industrial Internet of Things (IIoT).
Tune in to future issues for more history, including explorations of oil analysis as a condition monitoring field, the evolution of sampling methods and test selections, the spread of oil analysis labs throughout North America and the development of many other technologies, including viscometry, particle counting titration, gas chromatography, flash-point testing, blotter spot chromatography, grease analysis and more.
We will also cover some of the early pioneers in the field of machinery lubrication — in the next part of our series, we will be covering Elijah McCoy, who invented lubrication systems for steam engines.
References
- Hansen, T. (March 2004). A Tribute to Vernon C. Westcott, Inventor of the Ferrograph. Practicing Oil Analysis.
- Johnson, M. (June 2007). Oil Analysis Past, Present & Future Part 2. Tribology & Lubrication Technology, 32-40.
- Johnson, M. (May 2007). Oil Analysis Past, Present & Future Part 1. Tribology & Lubrication Technology, 32-39.
- Poley, J. (2019). Practical Fluid Analysis in the 21st Century. Ft. Myers, FL: Reliabilityweb.com.