Understanding and Detecting Shear-Stress Induced Deposits
Introduction
Imagine a multi-stage compressor train in a petrochemical facility that has one lubricant sump feeding multiple journal bearings. Your oil analysis indicates that the fluid is in ideal condition, with Membrane Patch Colorimetry (MPC) in the single digits, Rotating Pressure Vessel Oxidation Test (RPVOT) close to new oil levels, and no significant contamination present. However, one of the journal bearing temperatures begins to peak, and over time, the temperature trends resemble a saw-tooth pattern, with each peak increasing in temperature. Before long, the temperatures approach the alarm limit, and if left unchecked, an outage may be required.
The problem is that there is not a scheduled outage for 36 months and bringing the compressor down will cost millions in lost production. You take moreadvanced oil samples, but everything appears to be fine. In this scenario, many operators assume that a mechanical issue is at play, and they closely monitor vibration sensors while calling on OEM and expert consultants to help identify the source of the temperature fluctuations.
This is a common experience for those who have encountered turbine oil severe shear-stress and the resulting localized deposits, also known as hot varnish. This paper will examine this phenomenon and offer suggestions for detecting and remedying it.
“Traditional” Varnish Formation
Lubricant varnish is a well-studied topic in turbomachinery. It is widely known that as lubricant oil degrades, it generates harmful by-products. Although oxidation is the most common degradation mechanism, there are various other pathways leading to degradation and the generation of by-products.
These polar degradation products are not stable in the non-polar oil phase and tend to come out of solution, forming deposits. The associated reliability problems with turbomachinery are well-documented. For example, deposits may cause valves to stick, resulting in unreliable control of turbines and potential trip events.
Varnish formation in hydrogen seals can lead to premature failure, while heat exchangers coated with deposits experience a loss of efficiency. Deposits on bearings can cause accelerated temperatures and increased wear rates.
Fig. 1 depicts the common understanding on the process of varnish formation. As the lubricant oil degrades, by-products are produced, which eventually transition from being in solution to suspension, settling out of the oil. Degradation products are soluble, at least in turbomachinery applications, and can move in and out of solution.
Soluble degradation products can be proactively measured using the MPC (ASTM D7843) and Ultra Centrifuge (UC) test. This can help turbomachinery operators take corrective actions before reliability problems arise. This common type of varnish, also known as "cold varnish,” forms during a cooling phase in the lubricant and settles out in cool or low flow areas.
However, what happens when varnish forms under a different mechanism producing localized bearing deposits? What if oil condition monitoring tests are no longer effective at predicting this formation? In short, more reliability problems.
Shear-Stress Degradation
Severe shear-stress is a degradation pathway that affects the lubricant in certain turbomachinery applications, particularly those operating at high speeds and under heavy load. Shear-stress is characterized by the transformation of mechanical energy into thermal energy as the shearing force increases, resulting in the generation of high localized temperatures.
In certain turbomachinery applications, the molecular friction generated from shear-stress can result in temperatures reaching several hundred degrees Celsius (Chu Zhang, 2017), leading to instant degradation and the formation of localized deposits. These high temperatures are isolated and localized in the minimum oil film thickness zone, occurring at a molecular level (Yulong Jiang, 2021).
Research of the “Morton Effect”, the phenomenon of synchronous rotor instability due to nonuniform heating of journal bearings, is also said to be caused by shear-stress. The Morton Effect causes vibration issues in turbomachinery. Shear-stress is a dominant factor in the generation of nonuniform bearing temperatures. (Jongh, Sept 17-20, 2018)
Directly observing the behavior of turbine oil during operation is not feasible due to the extremely thin oil film, which can be as low as a few microns and may support a several-ton journal bearing rotating at thousands of revolutions per minute. Detecting temperature inside the oil is also not possible, but it is possible to obtain hints about the temperatures reached by analyzing bearing deposits.
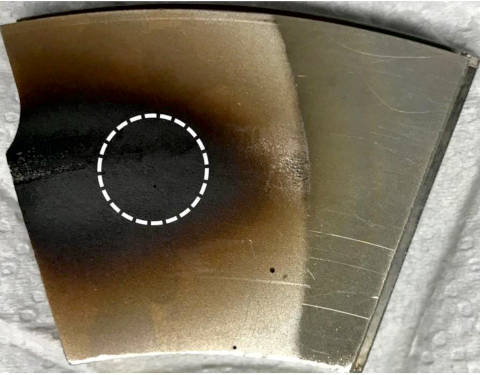
Figure 2 shows a varnish-coated bearing pad that had multiple deposit samples extracted from the varnish layer across the surface of the bearing. The majority of the deposits are organic, oxidized oil degradation products. However, the darkest deposit hue can consist of an inorganic, like phosphorus-based Extreme Pressure (EP) additive. Typically, EP additives do not react until temperatures of about 200°C are reached. This phosphorus-rich deposit suggests that the oil had temperatures at least this high, forming these localized deposits. It is important to note that these micro-temperature zones are not detected by the bearing thermocouple probes.
In this example, phosphorus is an indicator of temperature, but in oils without phosphorus, the same phenomenon can occur.
The Impact of Shear-Stress Deposits
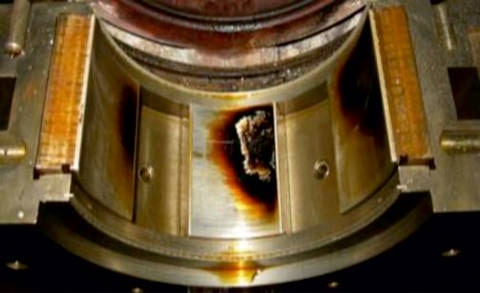
The carbonization of the oil and subsequent deposit formation impacts the performance of the bearing in three significant ways. First, the deposits act as an insulator, reducing the oil’s ability to cool the bearing. This results in bearing temperature excursions, sometimes reaching trip alarm levels. Second, varnish layers act like surface asperities impacting the oil to maintain a solid hydrodynamic wedge.
In some cases, the wedge may crack, temporarily allowing metal to metal contact resulting in bearing wear. Therefore, varnish deposits may be accompanied by metal scoring and wear, as can be seen in the pictures below. Third, bearing deposits may induce vibrations, as described by the Morton Effect.
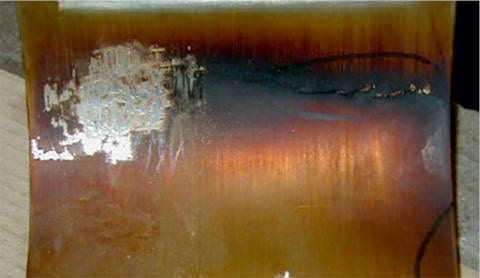
Detecting Shear-Stress Deposits
One of the biggest challenges with shear-stress deposits, or hot varnish, is that because the degradation occurs at a localized level and immediately sticks to metal components, the bulk oil doesn’t become sufficiently polluted to detect with oil analysis. In many cases, MPC and UC tests identify no issue, so other condition-monitoring technologies are necessary. Trending bearing temperatures has been shown to be the most reliable of detecting bearing deposits. The signature of a temperature trend often resembles a sawtooth pattern, as can be observed below in Fig. 5.

In general, bearing temperature spikes (independent of load) indicate varnish. While an increasing sawtooth pattern is almost a sure sign of varnish, it can be detected with even a stable sawtooth form.
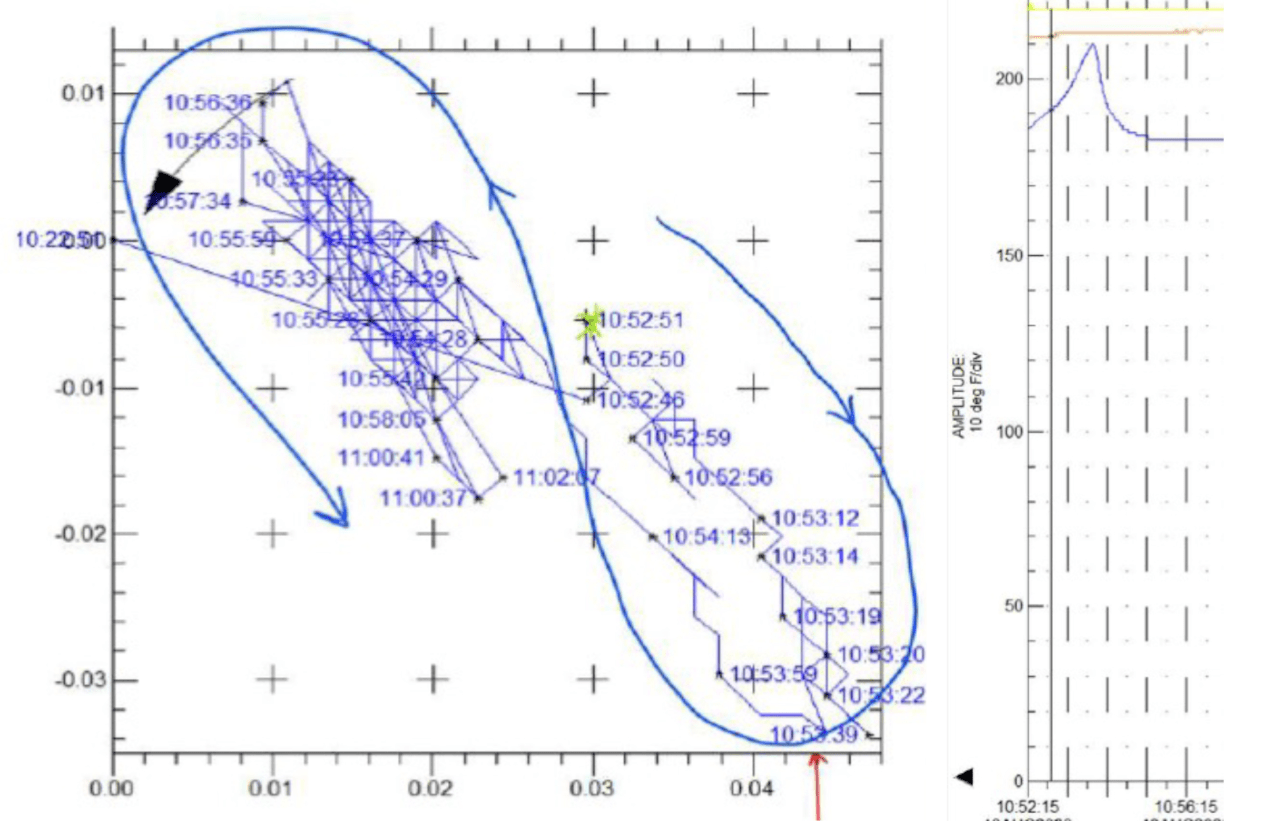
Shear-stress deposits exhibit inherent catalytic properties. Their formation leads to elevated bearing temperatures, decreased clearances, and an amplified likelihood of further shear-stress occurrence.
The film strength of the varnish can be sufficient to move the entire shaft. For those systems running with instrumentation measuring the shaft position, such as a gap voltage vertical probe, one may observe the shaft moving away from the center as the temperature increases and then resuming to its normal position as the temperature drops. This can be observed in Fig. 6:
These deposits are detected by the shape of the temperature plot, and then also observed in the movement of the shaft. Figure 7 presents a concise overview of noteworthy bearing temperatures based on the API 670 thermal couple location. These temperatures are anecdotal norms, but specific machines can experience very different norms.
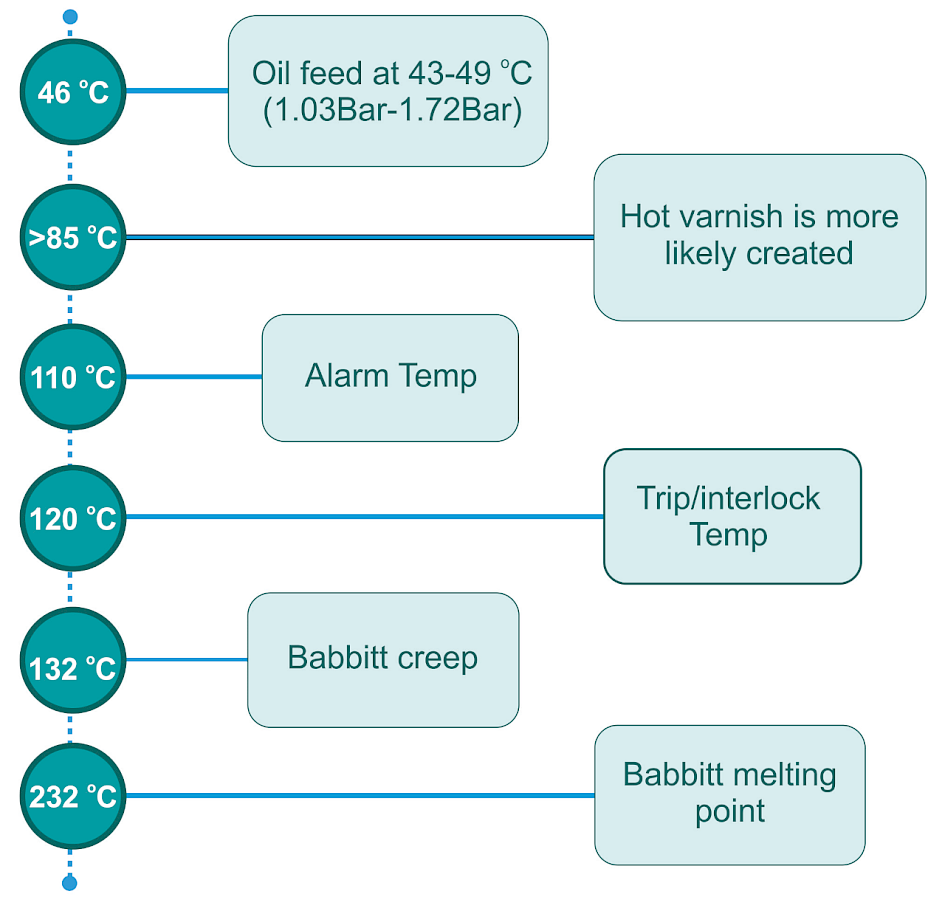
The Factors Influencing Shear-Stress Degradation
The two dominant factors that can influence shear-stress degradation are a bearing’s load and rotational speed, as illustrated in Fig. 8. Bearing deposits occur in the minimum oil film thickness because this corresponds to the highest load zone of the bearing.
Shear-stress deposit events occur more frequently in compressors than in turbines. Turbines typically operate at 3,600 rpm in the 60Hz North American market and 3,000 rpm in Europe and Asia Pacific, where the power grid operates at a frequency of 50 Hz. Compressors on the other hand can see bearings operate at an order of magnitude higher, sometimes greater than 50,000 rpm.
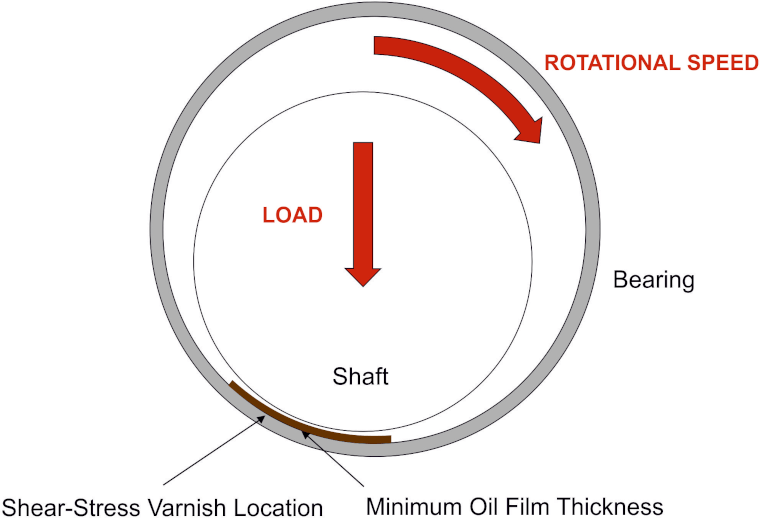
Potential Ways to Mitigate Shear-Stress
Will switching to a different turbine oil help remedy shear-stress deposits? The model to determine shear-stress is complex and still to be defined. Various turbine oil formulations have not been tested in a controlled setting to compare performance. However, anecdotally, bearing deposits due to shear-stress have been observed in Group I, II, III and IV base oil formulations, suggesting that simply changing to a new base-stock formulation will not provide a solution.
Advances in EP-gear load additives combined with additive dispersions that have been blended in higher quality base oils have proven to minimize the impact of shear-stress in high-speed bearing applications.Managing deposits due to shear-stress can be addressed mechanically in the turbine by decreasing the load on the oil. This may be accomplished by the following mechanical fixes which have been observed to work:
- Reduce load (operationally feasible but reduces compressor output)
- Opening bearing clearances (Jongh, Sept 17-20, 2018)
- Offset bearing pivot towards its lagging side can improve the angle of attack and allow more oil flow
- Directional lubricating
Although shear-stress degradation is fundamentally a mechanical issue, it may also be possible to address these deposits from a chemical perspective. The use of Mobil™ Solvancer®, an oil soluble cleaner, has been shown to have an immediate impact on deposit formation and often results in significant drops in bearing temperature. The product is also developed for long-term use, ideally providing a long-lasting solution to bearing deposits.
Mobil Solvancer® effectively mitigates deposit formation by enhancing the solubility of the in-service oil, enabling the dissolution of degradation byproducts. Varnish deposits can be comprised of depleted antioxidants, inorganic additives, and degraded hydrocarbon molecules. Mobil Solvancer® also softens carbon-based deposits, which can act as the glue holding an inorganic deposit like phosphorus onto the journal bearing, and then helping to remove the deposit.
These varnish deposits, when dissolved in the oil, remain inert and pose no operational concerns until they precipitate out of solution. Consequently, the process of dissolving these deposits back into the oil does not have any adverse impact on the oil's condition nor does it pose a risk of catalyzing further degradation.
An example of the impact of adding Mobil Solvancer® to a compressor suffering from shear-stress deposits can be seen in Fig. 9. After a 5% addition of Mobil Solvancer, the bearing temperature excursions stopped over the course of a few hours.
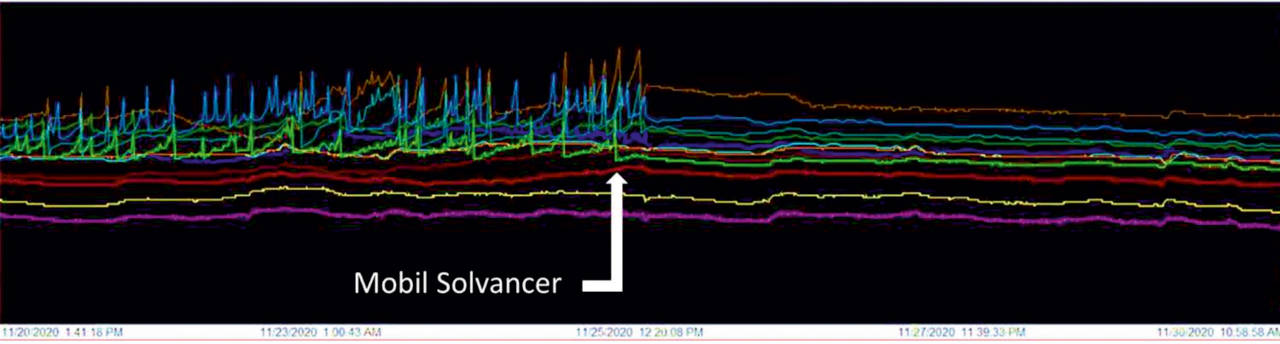
Although it is not always possible to overcome mechanical issues through chemistry, Mobil Solvancer® is one cost-effective option to consider if bearings are suffering from shear-stress deposits.
Conclusion
Varnish deposits in journal bearings pose a serious threat to the reliable operation of turbomachinery, as they can lead to increased temperatures and wear rates. Typically, varnish is predicted through oil-analysis tests, such as the MPC or UC test. However, a degradation mechanism called shear-stress can create very high temperatures, resulting in localized deposits. These deposits can occur even when most of the oil is in adequate condition and traditional varnish tests do not forecast a problem. The best way to detect shear-stress induced deposits is by monitoring bearing temperatures and vibrations.
If bearing temperatures are increasing due to shear-stress, mechanical fixes may be employed to spread the bearing load over more oil to reduce load and improve cooling. Additionally, Mobil Solvancer®, an oil-soluble cleaner, has been found to be effective, with an immediate impact on reducing bearing temperatures.
Note: The term Shear Stress Deposits (SSD) was suggested to the authors by Noria’s Jim Fitch in March, 2023. It is descriptive of the thermal distress induced from severe intermolecular friction leading to localized deposit formation. A common name for this phenomenon in the industry is “Hot Varnish”.
References:
- Chu Zhang, J.-G. Y.-S. (2017). Influence of Varnish on Bearing Performance and Vibration of Rotating Machinery. International Journal of Rotating Machinery, Article ID 9131275, 10 pages.
- Jongh, F. d. (Sept 17-20, 2018). The Synchronous Rotor Instability Phenomenon - Morton Effect. 47th Turbomachinery & 34th Pump Symposia, Houston, Texas, 12.
- Yulong Jiang, B. L. (2021). Prediction on Flow and Thermal Characteristics of Ultrathin Lubricant Film of Hydrodynamic Journal Bearing. Micromachines, 12, 1208.