Advertorial: OEE- Overall Equipment Effectiveness
Industrial Lubricants improve productivity under company technology leadership and application expertise. But what is really meant by "improving productivity"? How can productivity be defined? For years the company has talked about lower total cost of ownership, reducing unscheduled downtime and improving maintenance practices, but how do those concepts impact a customer's productivity, and in turn, profitability? Do they really matter?
One prevailing industry measure of productivity is Overall Equipment Effectiveness, OEE. Simply stated OEE is a measure of the productivity of an asset. If a machine has a planned production of 10 hours, with the expectation that it can produce 8000 units during that time, but the machine only produces 6300 units during the shift, that machine has an OEE of 79% (6300 / 8000 = .7875). But what does that mean, and how can Industrial Lubricants help increase that number?
The Components of OEE
To answer this question, you must understand the three components that make up OEE. hese components are defined as Availability, Performance, and Quality. These three dimensions are measured individually and combined to create a total OEE.
Availability measures how frequently a machine is available for its intended use. Events that stop a machine's production result in a down time loss. Availability can be affected by equipment failure, unplanned maintenance and downtime, material shortages, and machine changeover times.
Performance is more difficult to assess, but is defined as a speed loss. If a machine is rated to produce a certain amount of units per hour, and runs uninterrupted for that hour, producing fewer units than the machine's rating is defined as a performance loss. These losses can be attributed to machine wear, operator inefficiency, substandard materials, or material misfeeds.
Quality is probably the easiest of the three components to quantify. Quality can be calculated simply by measuring the amount of scrap a machine produces. Any reject material, pieces that don't meet quality standards, and rework all contribute to quality losses.
OEE Example
Here is an example of an OEE Calculation, based on the information one operator may record.
The plant shift is 8 hours, with two planned 15 minute breaks and a 30 minute meal break. The injection molder in question can produce 30 pieces per minutes at its ideal cycle time. The machine is down for 38 minutes of the shift, but produces 9,723 pieces during its uptime. 207 of these are rejected and sent for regrinding. Just based on this information we can calculate OEE…
8 hours | 480 minutes |
Breaks | 60 minutes |
Downtime | 38 minutes |
Parts Produced | 9723 |
Rejects | 207 |
Rating (pieces per minute) | 30 |
Planned Production Time | 480 - 60 = 420 |
Operating Time | 420 - 38 = 382 |
Availability | 382 / 420 = 0.910 |
Performance | (9723 / 382) / 30 = 0.848 |
Good Pieces Produced | 9723 - 207 = 9516 |
Quality | 9516 / 9723 = 0.979 |
OEE | 0.910*0.848*0.979=75.5% |
This machine had an OEE of 75.5% this shift.
Measuring OEE
Now that we understand OEE, we need to be able to measure it to track improvements. Availability is computed as a ratio between actual operating time and planned production time.
Availability = Operating Time Planned Production Time
Performance is the ratio of the ideal cycle time to the operating time divided by total pieces produced.
This can also be defined as a ratio of Net Operating Time to Operating Time.
Quality is measured as the ratio of good pieces to Total pieces.
How Mobil Industrial can help improve OEE
Many of the areas Mobil Industrial Lubricants has focused on for years are also key drivers of improving OEE. We know that higher quality lubricants can lead to lower total cost of ownership by reducing unscheduled downtime, increasing machine and component life and extending maintenance intervals.
Let's look at how these can drive higher OEE. In an injection molding machine, a malfunctioning servo valve can cause an unscheduled machine shutdown, and cost up to a half hour of machine availability. A blower breakdown can create difficulties getting raw materials into the machine hopper, interrupting production. Unplanned events such as these drive down machine availability, and correspondingly, OEE. By using Mobil Industrial Lubricants and an oil analysis program, you can reduce equipment failures and better predict service life, allowing you to increase your machine's availability.
You can also drive performance by uUsing sing high quality lubricants and maintenance practices. A hydraulic system that has pump wear, deposits, and varnish will not operate at its rated performance level, with decreasing speed and pressure as a result. Mobil premium hydraulic oils have been proven to offer outstanding contamination control, exceptional wear protection, and cleanliness that lasts. These critical characteristics, combined with monitoring the system with an oil analysis program can help keep your machines performing at their highest level.
Quality can also be directly impacted by the lubricants in use. Malfunctioning ejector pins can cause parts to stick inside the mold, sending them to the scrap heap for regrinding. Poor hydraulic clamping pressure can have the same effect. All of these losses can mount, seriously impacting overall productivity. Using Mobil SHC grease can reduce ejector pin wear, reducing your quality losses.
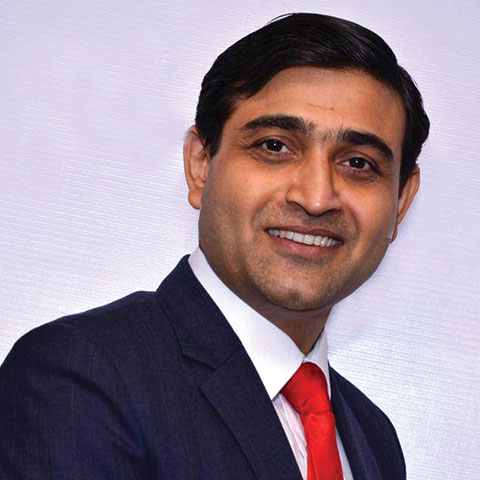
About the Author
Shankar Karnik joined Indo Mobil Pvt. Ltd. Industrials in 1998. Following its merger with Exxon, he was appointed Business Development Manager – Power. He developed the Industrial lubricants business, going on to oversee the North & West India markets, with the marine lubricants business added. Karnik is currently General Manager, Industrial at ExxonMobil Lubricants Pvt Ltd.