Rationalization of Lab Tests for Measurement of Insoluble Contaminants in Lube Oil
Lubricants are essential and expensive components of machine systems and need sampling, analysis and monitoring. Monitoring can be either performance testing or oil condition monitoring. Knowledge of the system’s critical failure modes is essential for cost-effective oil and machinery monitoring. The determination of insoluble contaminants in lube oil is one of the parameters usually recommended for evaluating the condition of in-service lube oil. The present study provides a comparative evaluation of two different tests that measure insoluble contaminants in lube oil. The objective of this study is to compare existing tests and adopt the most effective test to be used for the measurement of insoluble contaminants in lube oil. The first test utilizes the gravimetric method through a filter (filter test) to measure the weight of insoluble contaminants, while the second test utilizes centrifugal forces at high speeds (ultra-centrifuge) for measurement. A total of 305 different lube oil samples were used in this study for both tests, where the results are critically analyzed and compared against each other. In addition, the tests are evaluated in terms of efficiency as well as safety.
Introduction
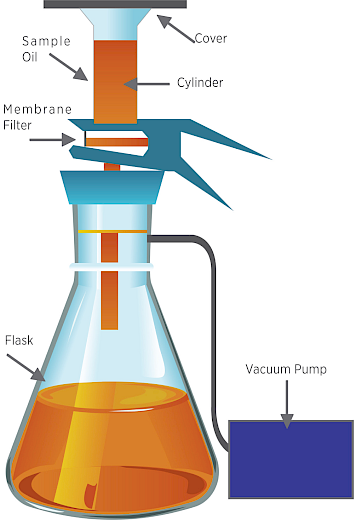
Lubrication oil is an important information source for early machine failure detection, just like the role of human blood sample testing in performing disease detection. The condition of lubrication oil and its circulation system reflect the health status of the machinery and its components. Contamination in lube oil is the major cause of rotating equipment failures in industry. The impact of this contamination is exponential on equipment reliability over time. The lube oil degradation can be the result of both physical and chemical actions, internally generated or from extraneous contaminations. It should be remembered that lubricants are usually complex blends of chemical additives in a variety of base oils. Since these finished lubricants are often specifically designed for particular applications, exposure of lubricants to conditions and component materials for which they are not intended may accelerate lubricant deterioration and result in equipment damage. Contamination control is the paramount factor needed to ensure equipment reliability and preserve system integrity. Therefore, it is critical to identify the presence of contaminants to eliminate potential catastrophic equipment failure by means of implementing timely corrective action. There are different test methods used in industry to measure contaminants in lube oil. Currently, two test methods are utilized for measuring insoluble contaminants, and these tests are part of the regular test slate for specific types of lube oil testing. The insoluble contaminants in hydraulic, transmission, refrigeration and synthetic turbine oils are measured by the gravimetric method (filter test), whereas the remaining oils are measured through high-speed centrifuge (ultra-centrifuge) analysis. As the objective for both tests is identical, it was decided to evaluate both test methods by correlating their results, with the goal of keeping only one test to measure the insoluble contaminants in lube oil, irrespective of the lube oil type. The study was conducted for the replacement of filter analysis by ultra-centrifuge (UC) test to determine insoluble contaminants by performing simultaneous analysis, i.e., gravimetric and centrifugal methods on various lube oil samples.
Methodology
The popular test methodologies being followed in the laboratory for measuring insoluble contaminants in lube oils are:
1. Gravimetric Analysis
This test method covers the determination of insoluble contamination in lube oils by gravimetric analysis. The contamination determined includes both particulate and gel-like matter, organic and inorganic, which is retained on a membrane filter disk. Insolubles in lube oil are determined by a known volume of the sample filtered through pre-weighed 1.2 µ filters, and then the increase in weight is determined after washing and drying the filter. The total contaminant content of the particular sample is determined by the increase in the weight of the filter. This is a manual method, and the technician is exposed to two solvents: kerosene for dissolving oil and petroleum ether to remove oil from the filter. This is a time-consuming process.
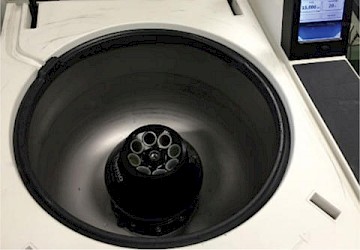
2. Centrifugal Method
A small amount of lube oil sample in a test tube is run for 30 minutes at 17,000 RPM in a refrigerated ultra-centrifuge. By subjecting the sample to G-forces, the insoluble contaminants can be extracted with different sizes or densities at controlled temperatures. The density of the agglomerated material at the bottom of the test tube is visually compared to a reference chart. The shapes in the reference chart reading range from 0 (the cleanest) to 8 (the most contaminated). When the UC value exceeds 2, a marginal condition is noted. A UC value exceeding 5 is considered to be a critical result. In this method, no solvent is used, and sample processing is not required to determine the contamination level.
Pros & Cons
The pros and cons for both discussed methodologies are listed here:
Methodology | Pros | Cons |
---|---|---|
Gravimetric Analysis | Relatively cheap tools | Time-consuming |
Results are based on weight, hence cannot be misinterpreted | Manually operated procedure | |
Exposure to kerosene and petroleum ether | ||
Centrifugal Method | Automated procedure | Expensive equipment |
Minimum manual input required and time-saving | Scale rating is judged visually and is prone to human error | |
Can test multiple samples simultaneously | Prone to maintenance issues | |
No chemicals needed |
Insoluble Contaminants Measurement | |
---|---|
Gravimetric Method (mg/liter) | Utra-Centrifuge |
0 to 50 | 0 |
51 to 80 | 1 |
81 to 120 | 2 |
121 to 150 | 3 |
151 to 175 | 4 |
175 to 200 | 5 |
201 TO 280 | 6 |
281 to 360 | 7 |
>360 | 8 |
Results and Discussions
There were 305 lube oil samples from hydraulic, transmission, refrigeration and synthetic turbine oils, which were analyzed simultaneously for insoluble contamination by both gravimetric and UC methods. The results are compatible and show linearity by both methods. The comparison of insoluble contaminants in the analyzed 305 lube oil samples showed that the results by gravimetric method vary from 2 ppm to 414 ppm, whereas UC values lie between 0 and 8. Three samples deviated from linearity, but they were positive in the crackle test and had high water content. The results of these three samples were not considered in determining the equivalency of values obtained by both methods. The equivalency of contaminants/insoluble determined by both methods was critically analyzed and classified as per the graph in Figure 3 and Table 2.
Conclusions
Experimental data were critically analyzed, and the results from both methods were compatible and had a linear correlation. The filter test involves the potential of hazardous solvent exposure for the lab technician. It is a time-consuming process, as it needs the preparation of every sample to carry out the test. In contrast, the ultra-centrifuge does not require any hazardous solvent, and multiple samples can be tested at a time. The hazards associated with handling kerosene and petroleum ether are: Petroleum ethers are extremely volatile, have very low flash points, and present a significant fire hazard. Exposure to petroleum ether occurs most commonly through inhalation or skin contact. The inhalation of kerosene fumes might cause dizziness or nausea. The mentioned solvents used in the filter test are consumable. Therefore, it is recommended to adopt the ultra-centrifuge for measuring insoluble contaminants for all samples, as this method is safer and faster than the filter test.
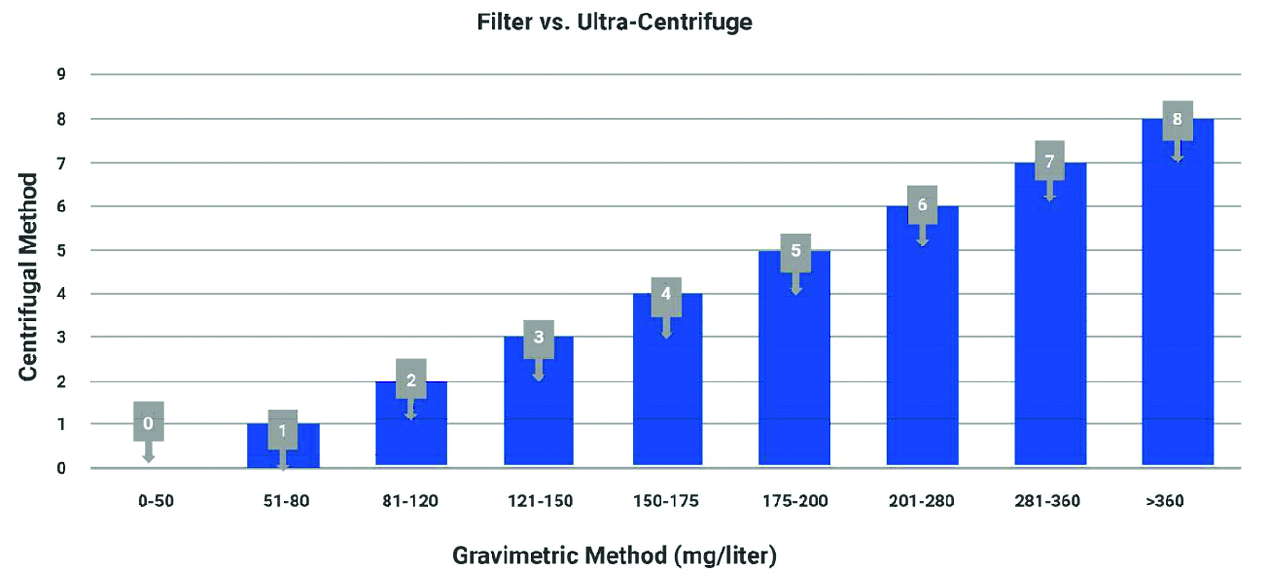
Reference
1. Knochen, M., Sixto, A., Pignalosa, G., Domenech, S., Garrigues, S., & De La Guardia, M. (2004). Determination of insolubles in diesel lubricating oil by FIA-visible spectrometry. Talanta, 64(5), 1359-1363.
2. Abner Jr, E. (1983). Lubricant deterioration in service. CRC Handbook of Lubrication, Citeseer, 517-532.
3. Zhu, J., He, D., & Bechhoefer, E. (2013). Survey of lubrication oil condition monitoring, diagnostics, and prognostics techniques and systems. Journal of chemical science and technology, 2(3), 100-115.
4. Toms, A., & Toms, L. (2010). Oil analysis and condition monitoring. In Chemistry and technology of lubricants (pp. 459-495). Springer, Dordrecht. 5. Kon, T., Honda, T., & Sasaki, A. (2020). Estimation of the Oxidative Deterioration of Turbine Oil Using Membrane Patch Color. Advances in Tribology, 2020.